Hydraulic Clutch
- charliemccraney
- Posts: 1743
- Joined: July 9, 2008, 10:02 pm
- Location: Lawrenceville, GA
Hydraulic Clutch
I kinda started on this a couple years ago but ran into issues. They are outlined in the following thread.
http://www.slick60s.com/viewtopic.php?f=1&t=16971
If you don't want to read through that, I'll summarize. The master cylinder would not bolt to the firewall and even if it did, the new style plastic cap could not be removed to fill or check the fluid.
I noticed two other bolts on the firewall that also hold one part of the bracket that the master cylinder uses to mount. I loosened those two bolts and was able to move it enough so that the master cylinder now bolts on easily. Before I mounted it, I screwed on an older metal cap and it can be removed with the cylinder mounted.
This is my next unfinished project to finish and now that the major issues have been resolved, I'm going to get back on it.
http://www.slick60s.com/viewtopic.php?f=1&t=16971
If you don't want to read through that, I'll summarize. The master cylinder would not bolt to the firewall and even if it did, the new style plastic cap could not be removed to fill or check the fluid.
I noticed two other bolts on the firewall that also hold one part of the bracket that the master cylinder uses to mount. I loosened those two bolts and was able to move it enough so that the master cylinder now bolts on easily. Before I mounted it, I screwed on an older metal cap and it can be removed with the cylinder mounted.
This is my next unfinished project to finish and now that the major issues have been resolved, I'm going to get back on it.
Lawrenceville, Ga
1961 F100 Unibody
318 Y-block (292 +.070 bore, +.170 stroke), FMS T5-Z w/Mustang 10.5" diaphragm clutch.
1961 F100 Unibody
318 Y-block (292 +.070 bore, +.170 stroke), FMS T5-Z w/Mustang 10.5" diaphragm clutch.
- unibody madness
- Posts: 2140
- Joined: December 4, 2008, 4:33 pm
- Location: Paradise,CALIFORNIA 95969
Re: Hydraulic Clutch
Charlie,
Glad you are getting back to it.
I kind of blundered along on my own when you put the mod on the back burner.
I bought the clutch master for the 60 f100 with the four mounting bolts.
I had a spare stiffener plate, used behind the brake master at the fire wall.
That plate has four bolts through the fire wall and two bolts coming out into the engine bay that work as studs for the brake master.
I simply reversed the function of the plate, using the two bolts to mount through the wall, and the four to hold the clutch master.
It has a smaller plug type cap that can be removed in place, but filling it can be a pain because of the body lip just above it.
The peddle mods were also a bit tricky because the hole on the peddle shaft is a little to high and long. I welded a nub to the front of the peddle shaft, redrilled the hole and bent the plunger shaft a little to accomodate the swing angle
The clutch appears to work, however I have yet to break in the 292 so actual working ability is still unknown.
Thanks for reposting
John
Glad you are getting back to it.
I kind of blundered along on my own when you put the mod on the back burner.
I bought the clutch master for the 60 f100 with the four mounting bolts.
I had a spare stiffener plate, used behind the brake master at the fire wall.
That plate has four bolts through the fire wall and two bolts coming out into the engine bay that work as studs for the brake master.
I simply reversed the function of the plate, using the two bolts to mount through the wall, and the four to hold the clutch master.
It has a smaller plug type cap that can be removed in place, but filling it can be a pain because of the body lip just above it.
The peddle mods were also a bit tricky because the hole on the peddle shaft is a little to high and long. I welded a nub to the front of the peddle shaft, redrilled the hole and bent the plunger shaft a little to accomodate the swing angle
The clutch appears to work, however I have yet to break in the 292 so actual working ability is still unknown.
Thanks for reposting
John
Turk build thread at:
viewtopic.php?f=32&t=18944
It does not matter what you think, it only matters what you do about it!
viewtopic.php?f=32&t=18944
It does not matter what you think, it only matters what you do about it!
Re: Hydraulic Clutch
RHD slicks are hydraulic clutch from the factory and I happen to own one! 
I am wanting to take some pics of master/slave anyway because I think the slave is leaking and want to find suitable replacements. As you've already noted the new ones dont work properly. I want to avoid the new type anyway because the hydraulic lines and fitting are different.
I can post pics here if you need/want ideas or just want something a little more 'bolt up?'
I doubt the master slave combo is an australian exclusive item, other than tinkering with the mighty cleveland (and de-stroking it?!?!?) the aussies didn't do too much in the design/build department!!!

I am wanting to take some pics of master/slave anyway because I think the slave is leaking and want to find suitable replacements. As you've already noted the new ones dont work properly. I want to avoid the new type anyway because the hydraulic lines and fitting are different.
I can post pics here if you need/want ideas or just want something a little more 'bolt up?'
I doubt the master slave combo is an australian exclusive item, other than tinkering with the mighty cleveland (and de-stroking it?!?!?) the aussies didn't do too much in the design/build department!!!

- unibody madness
- Posts: 2140
- Joined: December 4, 2008, 4:33 pm
- Location: Paradise,CALIFORNIA 95969
Re: Hydraulic Clutch
Leeroy,
the slaves ar available you can even find them on ebay The masters are a bit harder to locate.
I would indeed like to see som pics of your set up.John
the slaves ar available you can even find them on ebay The masters are a bit harder to locate.
I would indeed like to see som pics of your set up.John
Turk build thread at:
viewtopic.php?f=32&t=18944
It does not matter what you think, it only matters what you do about it!
viewtopic.php?f=32&t=18944
It does not matter what you think, it only matters what you do about it!
Re: Hydraulic Clutch
Yes the slaves appear to be the same or similar to the fridge type.
I will get a pic of the master for you and post up. BEWARE tho, its original and damn dirty!
I will get a pic of the master for you and post up. BEWARE tho, its original and damn dirty!
- charliemccraney
- Posts: 1743
- Joined: July 9, 2008, 10:02 pm
- Location: Lawrenceville, GA
Re: Hydraulic Clutch
Leeroy,
Is the bore larger for the clutch master cylinder?
The NOS clutch cylinder I have has a 1 1/8" bore.
I took some measurements with the mechanical linkage and found that about 1 1/8" of clutch pushrod travel needs to equal about 1 1/4" of slave pushrod travel. Doing the math for the fluid displacement indicates 1 1/8" bore mc and 1" slave should work.
I found a new metal cap up the road at Mustangs Unlimited. The early Mustangs use a similar master cylinder. I also picked up some clutch/brake pushrod bushings from Melvins, also not far from me. I plan to figure out how I will do the hydraulic line this weekend and get some pics.
Is the bore larger for the clutch master cylinder?
The NOS clutch cylinder I have has a 1 1/8" bore.
I took some measurements with the mechanical linkage and found that about 1 1/8" of clutch pushrod travel needs to equal about 1 1/4" of slave pushrod travel. Doing the math for the fluid displacement indicates 1 1/8" bore mc and 1" slave should work.
I found a new metal cap up the road at Mustangs Unlimited. The early Mustangs use a similar master cylinder. I also picked up some clutch/brake pushrod bushings from Melvins, also not far from me. I plan to figure out how I will do the hydraulic line this weekend and get some pics.
Lawrenceville, Ga
1961 F100 Unibody
318 Y-block (292 +.070 bore, +.170 stroke), FMS T5-Z w/Mustang 10.5" diaphragm clutch.
1961 F100 Unibody
318 Y-block (292 +.070 bore, +.170 stroke), FMS T5-Z w/Mustang 10.5" diaphragm clutch.
Re: Hydraulic Clutch
Hi,
I didn't actually check the bore size sorry (and honestly not sure how to once its on the car?) I have the thick firewall sound deadener so I cant get the calipers into the bore whilst its on the car.
The slave is identical to the fridge type, the info I found was that slave cylinder was for a fridge is 1" bore slave also.
The mustang non power ones you refer to are 1".
Hmmmmmm, I was about to order another master as I want to change them both out, not so sure now!!!
I didn't actually check the bore size sorry (and honestly not sure how to once its on the car?) I have the thick firewall sound deadener so I cant get the calipers into the bore whilst its on the car.
The slave is identical to the fridge type, the info I found was that slave cylinder was for a fridge is 1" bore slave also.
The mustang non power ones you refer to are 1".
Hmmmmmm, I was about to order another master as I want to change them both out, not so sure now!!!
Re: Hydraulic Clutch
Just having a browse, did fruit jar masters come in 1 1/8" bore? Not saying that they didn't, but I cant seem to find one even as a replacement.
That would narrow it down if there was no such thing!
That would narrow it down if there was no such thing!

- charliemccraney
- Posts: 1743
- Joined: July 9, 2008, 10:02 pm
- Location: Lawrenceville, GA
Re: Hydraulic Clutch
What I've seen for the fridge indicates 1 1/16" bore. A different pedal ratio could be at play, too. I think Tim runs a fridge clutch master on the LSR Unibody and it does seem to work.
I think any combination will work. You have some fudge factor in the clutch linkage, anyway. A 1" bore mc will move the 1" bore slave about 1 1/8" which is probably within the design limits for the clutch.
I own one, so yep, they did come in 1 1/8"
I think any combination will work. You have some fudge factor in the clutch linkage, anyway. A 1" bore mc will move the 1" bore slave about 1 1/8" which is probably within the design limits for the clutch.
Leeroy wrote:Just having a browse, did fruit jar masters come in 1 1/8" bore? Not saying that they didn't, but I cant seem to find one even as a replacement.
I own one, so yep, they did come in 1 1/8"
Last edited by charliemccraney on March 5, 2015, 4:14 pm, edited 1 time in total.
Lawrenceville, Ga
1961 F100 Unibody
318 Y-block (292 +.070 bore, +.170 stroke), FMS T5-Z w/Mustang 10.5" diaphragm clutch.
1961 F100 Unibody
318 Y-block (292 +.070 bore, +.170 stroke), FMS T5-Z w/Mustang 10.5" diaphragm clutch.
- charliemccraney
- Posts: 1743
- Joined: July 9, 2008, 10:02 pm
- Location: Lawrenceville, GA
Re: Hydraulic Clutch
Alright, I've been real lazy, but I have made some progress.
The bolts on the firewall that you may need to loosen in order to move the bracket so that the master cylinder will bolt on:
Just above the master cylinder bolt
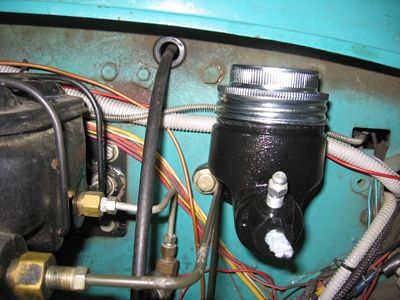
Below the master cylinder bolt, and directly in line with the others, just a hole in this picture as the bolt is removed temporarily.
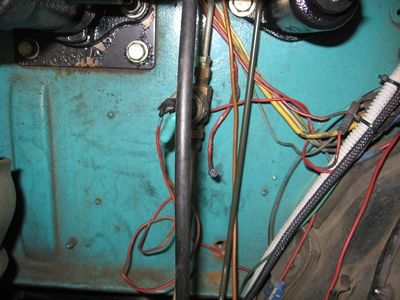
The plastic cap that came with the master cylinder is too tall. I found a metal one at Mustangs Unlimited, right up the road from me. It is short enough and an excellent quality repro. I don't know if the zinc plating is actually correct for anything, but the detail is excellent compared to my rusty originals.
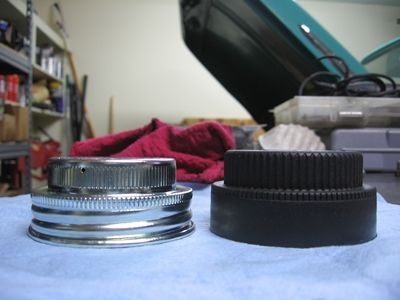
I have a hydraulic clutch pedal, which appears to be a mirror image of the brake pedal, but I had modified and painted a manual clutch pedal before I found the hydraulic pedal in a dump truck. I need something to hook the return spring so I ground two flats on a stainless bolt using an angle grinder with a cutoff wheel and drilled a hole. Hopefully it works out.
The clutch pedals are virtually identical. The manual unit has a bracket welded in place for the clutch rod which partially covers the hole for the pushrod. That bracket has to be removed. And there is no return spring bracket, but the hole is there.
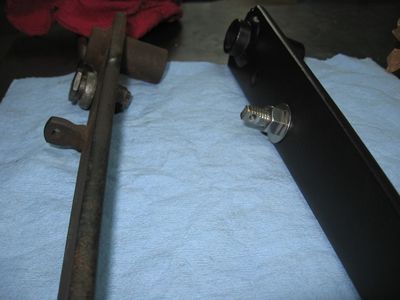
For whatever reason, the pushrod that I pulled from a hydraulic clutch equipped dump truck is too long so I'm going to try to use a brake pushrod. It also appears that the brake pushrods use a different bushing and is a little thicker where they mount to the pedal. I have several brake pushrods that were pulled from slicks and they are all the same.
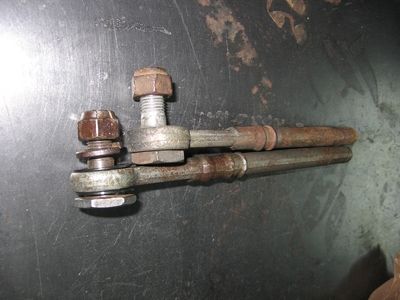
The bolts on the firewall that you may need to loosen in order to move the bracket so that the master cylinder will bolt on:
Just above the master cylinder bolt
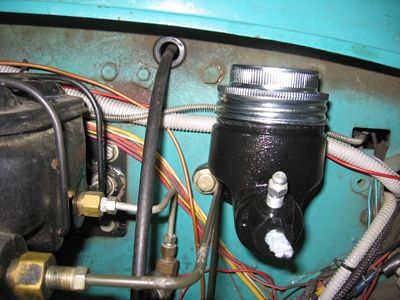
Below the master cylinder bolt, and directly in line with the others, just a hole in this picture as the bolt is removed temporarily.
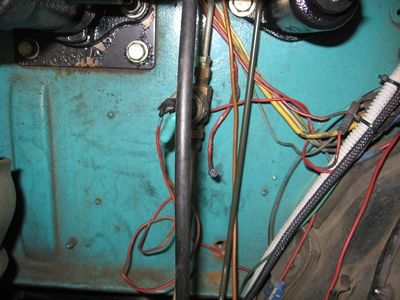
The plastic cap that came with the master cylinder is too tall. I found a metal one at Mustangs Unlimited, right up the road from me. It is short enough and an excellent quality repro. I don't know if the zinc plating is actually correct for anything, but the detail is excellent compared to my rusty originals.
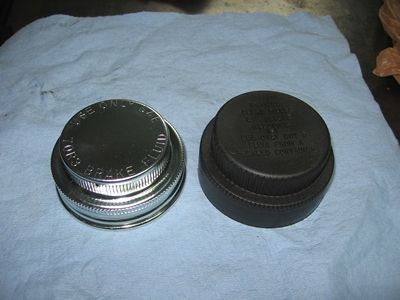
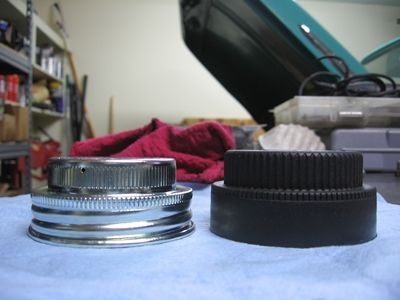
I have a hydraulic clutch pedal, which appears to be a mirror image of the brake pedal, but I had modified and painted a manual clutch pedal before I found the hydraulic pedal in a dump truck. I need something to hook the return spring so I ground two flats on a stainless bolt using an angle grinder with a cutoff wheel and drilled a hole. Hopefully it works out.
The clutch pedals are virtually identical. The manual unit has a bracket welded in place for the clutch rod which partially covers the hole for the pushrod. That bracket has to be removed. And there is no return spring bracket, but the hole is there.
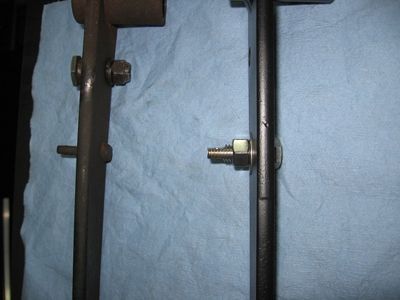
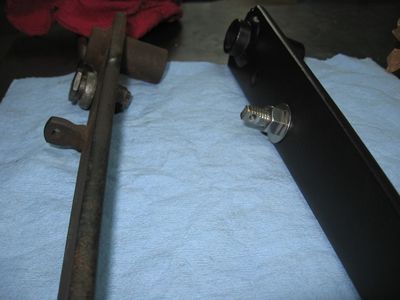
For whatever reason, the pushrod that I pulled from a hydraulic clutch equipped dump truck is too long so I'm going to try to use a brake pushrod. It also appears that the brake pushrods use a different bushing and is a little thicker where they mount to the pedal. I have several brake pushrods that were pulled from slicks and they are all the same.
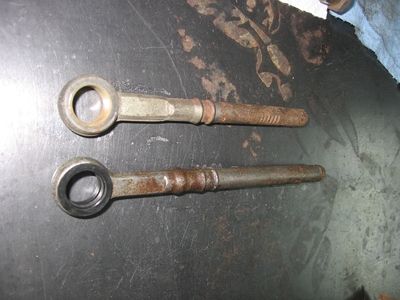
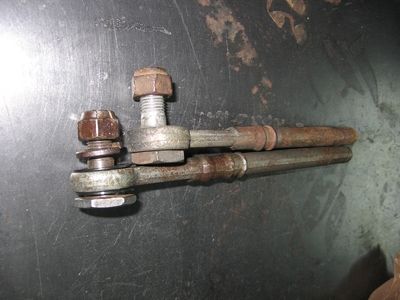
Lawrenceville, Ga
1961 F100 Unibody
318 Y-block (292 +.070 bore, +.170 stroke), FMS T5-Z w/Mustang 10.5" diaphragm clutch.
1961 F100 Unibody
318 Y-block (292 +.070 bore, +.170 stroke), FMS T5-Z w/Mustang 10.5" diaphragm clutch.
Re: Hydraulic Clutch
the pushrod that I pulled from a hydraulic clutch equipped dump truck is too long
Thats a common problem. Occasionally you can find a NOS master here in Australia and they always quote the supplied pushrod is for big slicks, must reuse your original for an F series.
Clutch pedal looks good!
- charliemccraney
- Posts: 1743
- Joined: July 9, 2008, 10:02 pm
- Location: Lawrenceville, GA
Re: Hydraulic Clutch
I decided to go with steel -4AN fittings and a stainless steel brake hose. Much easier than forming a line and flaring and it will handle the movement between the engine and body, but the hose does need something to hold it in place.
The best I can tell, the trucks that came with the hydraulic clutch used a 1/4" line from the factory and -4 AN is the equivalent. I also checked the id of the slave cylinder fitting area and it is larger than the id of a 3/16" brake line. The threads are also larger than a 3/16" brake fitting. The most significant possible problem I can think of with a smaller line is that it will not be able to move enough fluid quickly enough to allow the clutch to work properly.
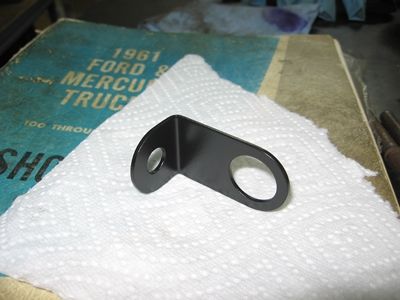
I used that lower bolt that fastens the dash bracket as the mounting point.
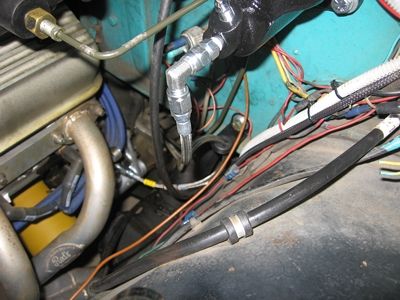
I wound up having to shorten a push rod. Even with the shorter brake pushrod, the pedal was far too high. I had one that had been cut previously so I made it work.
1st, the shortened pushrod, 4 3/8" center to end.
2nd, a stock brake pushrod, 4 5/8"
3rd, what I thought to be a clutch pushrod. Yet to be confirmed.
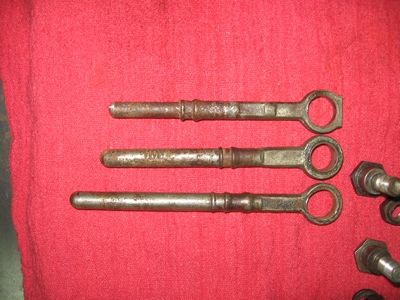
And... it works. It got me around the neighborhood and then around the block. The pedal is lighter and silky smooth and the clutch engagement seems much more positive. My mechanical linkage is in pretty good shape and I'd say it's a night and day difference, and worth the time.
There are still a few minor issues to overcome but nothing major. For instance, the clutch pedal rubber pad surface is smaller than all of the other pedals I have, so I'm probably going to paint the genuine hydraulic pedal I have and use it. It actually looks like the return spring is the exact same as the brake return spring, but I have an auxiliary fuse panel covering the mounting point, so I have to improvise until I address the rats nest of wires you see pictured. Like I said, nothing major.
In regards to the clutch pedal rubber pad, I wonder if the newer slicks use a smaller one and it is a newer pedal. I made a post inquiring about that here, http://www.slick60s.com/viewtopic.php?f=1&t=30686, if you know the difference, let me know on that post.
I'll post a parts list later for anyone who may want to do this.
The best I can tell, the trucks that came with the hydraulic clutch used a 1/4" line from the factory and -4 AN is the equivalent. I also checked the id of the slave cylinder fitting area and it is larger than the id of a 3/16" brake line. The threads are also larger than a 3/16" brake fitting. The most significant possible problem I can think of with a smaller line is that it will not be able to move enough fluid quickly enough to allow the clutch to work properly.
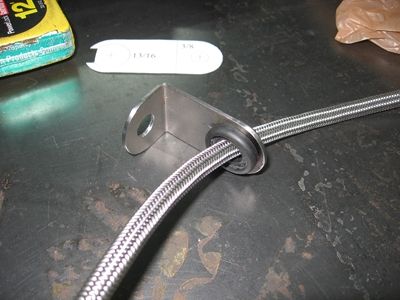
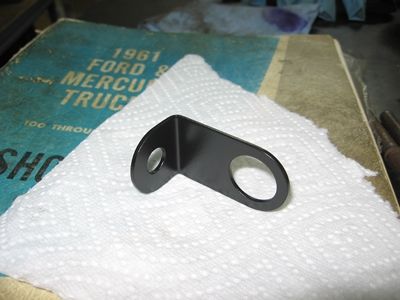
I used that lower bolt that fastens the dash bracket as the mounting point.
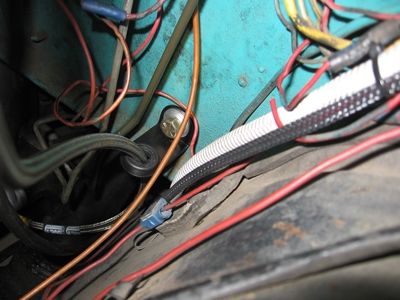
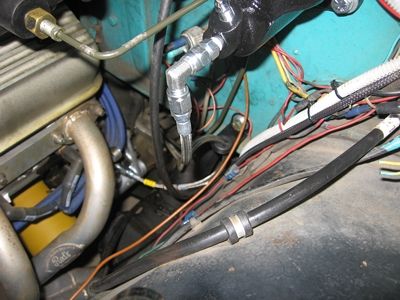
I wound up having to shorten a push rod. Even with the shorter brake pushrod, the pedal was far too high. I had one that had been cut previously so I made it work.
1st, the shortened pushrod, 4 3/8" center to end.
2nd, a stock brake pushrod, 4 5/8"
3rd, what I thought to be a clutch pushrod. Yet to be confirmed.
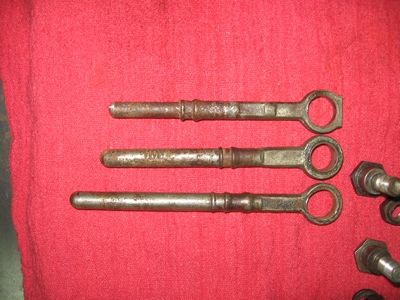
And... it works. It got me around the neighborhood and then around the block. The pedal is lighter and silky smooth and the clutch engagement seems much more positive. My mechanical linkage is in pretty good shape and I'd say it's a night and day difference, and worth the time.
There are still a few minor issues to overcome but nothing major. For instance, the clutch pedal rubber pad surface is smaller than all of the other pedals I have, so I'm probably going to paint the genuine hydraulic pedal I have and use it. It actually looks like the return spring is the exact same as the brake return spring, but I have an auxiliary fuse panel covering the mounting point, so I have to improvise until I address the rats nest of wires you see pictured. Like I said, nothing major.
In regards to the clutch pedal rubber pad, I wonder if the newer slicks use a smaller one and it is a newer pedal. I made a post inquiring about that here, http://www.slick60s.com/viewtopic.php?f=1&t=30686, if you know the difference, let me know on that post.
I'll post a parts list later for anyone who may want to do this.
Last edited by charliemccraney on July 14, 2013, 6:30 pm, edited 1 time in total.
Lawrenceville, Ga
1961 F100 Unibody
318 Y-block (292 +.070 bore, +.170 stroke), FMS T5-Z w/Mustang 10.5" diaphragm clutch.
1961 F100 Unibody
318 Y-block (292 +.070 bore, +.170 stroke), FMS T5-Z w/Mustang 10.5" diaphragm clutch.
- Uncle Skip
- Posts: 4695
- Joined: July 15, 2006, 8:30 pm
- Location: Pearland, Texas
Re: Hydraulic Clutch
BroncoTom is putting a wet clutch in the '65 for his M-5 transmission. We were looking at his pedal quadrant and decided he could put the lever arm on the same side as the gas pedal and move the master cylinder toward the center of the truck.
The shaft that mounts all the pedals goes all the way side to side and it has a "mounting boss" on both ends. He just guesstimated the angle required and welded the arm to the shaft.
So far, its worked out pretty good.
He had to cut a hole in the firewall, bolted a piece of flat sheet metal to the inside of the firewall and then the master to that flat piece. (I have a suggestion about that but I'll save it for later.)
That moved the master in about 3/8" closer to the lever and kept him from having to lengthen or make a new longer arm for the throw.
He's working on how to finish up the hole he cut but I'll try to sneak some pictures so you can see what I'm talking about.
It clears the 302 perfectly.
Just another idea for you all to consider if you'd like to plan a 5-speed overdrive transmission.
The shaft that mounts all the pedals goes all the way side to side and it has a "mounting boss" on both ends. He just guesstimated the angle required and welded the arm to the shaft.
So far, its worked out pretty good.
He had to cut a hole in the firewall, bolted a piece of flat sheet metal to the inside of the firewall and then the master to that flat piece. (I have a suggestion about that but I'll save it for later.)
That moved the master in about 3/8" closer to the lever and kept him from having to lengthen or make a new longer arm for the throw.
He's working on how to finish up the hole he cut but I'll try to sneak some pictures so you can see what I'm talking about.
It clears the 302 perfectly.
Just another idea for you all to consider if you'd like to plan a 5-speed overdrive transmission.
I'm not arguing with you. I'm just explaining why I'm right.
Pardon me. Does your deaug bite?
Pardon me. Does your deaug bite?
Re: Hydraulic Clutch
Its looking great! Glad it worked!
I know you are running a 1 1/8" master, did you end up running an 1" slave?
I ordered a new slave from macs 2 weeks ago and the one delivered was 1"
I know you are running a 1 1/8" master, did you end up running an 1" slave?
I ordered a new slave from macs 2 weeks ago and the one delivered was 1"
- charliemccraney
- Posts: 1743
- Joined: July 9, 2008, 10:02 pm
- Location: Lawrenceville, GA
Re: Hydraulic Clutch
The slave is 1". I don't think there is a size option for the slaves.
Lawrenceville, Ga
1961 F100 Unibody
318 Y-block (292 +.070 bore, +.170 stroke), FMS T5-Z w/Mustang 10.5" diaphragm clutch.
1961 F100 Unibody
318 Y-block (292 +.070 bore, +.170 stroke), FMS T5-Z w/Mustang 10.5" diaphragm clutch.
- charliemccraney
- Posts: 1743
- Joined: July 9, 2008, 10:02 pm
- Location: Lawrenceville, GA
Re: Hydraulic Clutch
Alright, Parts list.
C1TT-7A542-A Master Cylinder
33721 Slave Cylinder, from Advance Auto Parts
C5ZZ-2162-S Metal MC lid, zinc plated, from Mustangs Unlimited
From Summit:
EAR-591942ERL -4AN to 7/16-24 flare (1/4") adapter for slave
EAR-961604ERL -4AN to 1/8NPT adapter for master
EAR-966304ERL -4AN 90* swivel
EAR-64191922ERL -4AN 22" Stainless Brake Hose
GAR-J9047 Bleeder screws 3/8-24 x 1 1/8
From BMW
34 32 1 233 159 Actually a brake hose grommet for 70's Airhead motorcycles.
Additionally:
A bracket to hold the hose - you're on your own
A spare clutch pedal to modify or luck out and find a hydraulic pedal
A brake pushrod to modify
Possibly:
B7C2461A Brake and clutch pedal bushings
B2A2474A Pushrod Bushings
B7C2457A Rubber pedal pad
These are from the Melvin's catalog, here in Conyers, GA.
I think that's it.
C1TT-7A542-A Master Cylinder
33721 Slave Cylinder, from Advance Auto Parts
C5ZZ-2162-S Metal MC lid, zinc plated, from Mustangs Unlimited
From Summit:
EAR-591942ERL -4AN to 7/16-24 flare (1/4") adapter for slave
EAR-961604ERL -4AN to 1/8NPT adapter for master
EAR-966304ERL -4AN 90* swivel
EAR-64191922ERL -4AN 22" Stainless Brake Hose
GAR-J9047 Bleeder screws 3/8-24 x 1 1/8
From BMW
34 32 1 233 159 Actually a brake hose grommet for 70's Airhead motorcycles.
Additionally:
A bracket to hold the hose - you're on your own
A spare clutch pedal to modify or luck out and find a hydraulic pedal
A brake pushrod to modify
Possibly:
B7C2461A Brake and clutch pedal bushings
B2A2474A Pushrod Bushings
B7C2457A Rubber pedal pad
These are from the Melvin's catalog, here in Conyers, GA.
I think that's it.
Lawrenceville, Ga
1961 F100 Unibody
318 Y-block (292 +.070 bore, +.170 stroke), FMS T5-Z w/Mustang 10.5" diaphragm clutch.
1961 F100 Unibody
318 Y-block (292 +.070 bore, +.170 stroke), FMS T5-Z w/Mustang 10.5" diaphragm clutch.
- charliemccraney
- Posts: 1743
- Joined: July 9, 2008, 10:02 pm
- Location: Lawrenceville, GA
Re: Hydraulic Clutch
I got the hydraulic pedal painted. I also managed to remove the old rubber pad, and reinstall it without obliterating it which is good, because I think it looks better than the repro.
I also shortened the pushrod a bit more because the clutch pedal was a bit higher than the brake pedal. Now they are pretty close.
It's been working great.
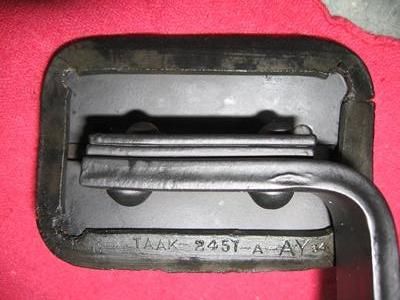
Number on the pad, TAAK-2457-A
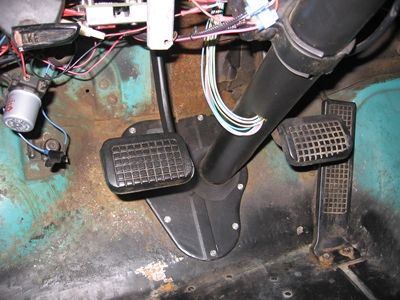
I also shortened the pushrod a bit more because the clutch pedal was a bit higher than the brake pedal. Now they are pretty close.
It's been working great.
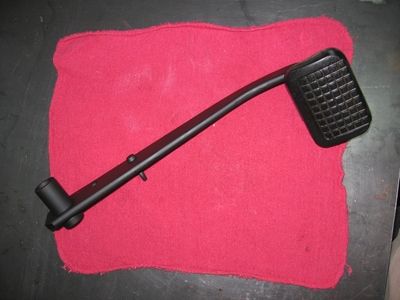
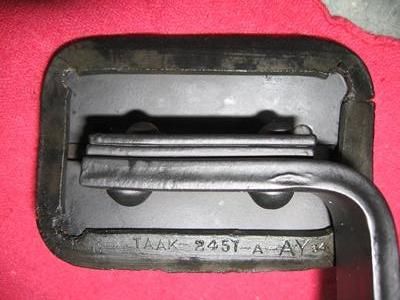
Number on the pad, TAAK-2457-A
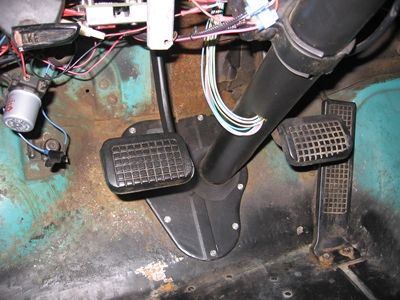
Lawrenceville, Ga
1961 F100 Unibody
318 Y-block (292 +.070 bore, +.170 stroke), FMS T5-Z w/Mustang 10.5" diaphragm clutch.
1961 F100 Unibody
318 Y-block (292 +.070 bore, +.170 stroke), FMS T5-Z w/Mustang 10.5" diaphragm clutch.
- charliemccraney
- Posts: 1743
- Joined: July 9, 2008, 10:02 pm
- Location: Lawrenceville, GA
Re: Hydraulic Clutch
I have switched to a modern hydraulic throwout bearing setup. The main reason is that my stock and aftermarket mix matched clutch parts didn't seem to play well together. A less significant reason is that the oem style hydraulic parts started leaking.
What was happening is that the clutch fork wears into the throwout bearing collar. The clutch I'm using is about 1/2" thinner than stock and I think that may be causing geometry issues and causing the wear. I think the fix for this is to have a longer or adjustable fork pivot stud made. Since the truck Y-Blocks use a 9/16 thread for the pivot stud, there is nothing from any other engine that I'm aware of that can work to do that. This means that stud would have to be custom, and therefore expensive. By itself, that is probably the way to go. However, because I had other issues, doing that to stick with the stock stuff wouldn't be very cost effective.
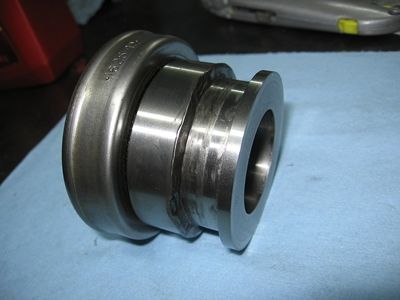
I got a master cylinder kit and hydraulic bearing from Tilton Engineering. There are others but for some reason, a lot of these bearings are indicated to not work with counterweight assisted pressure plates. Since that is what I have, Centerforce Dual Friction, it must work with that and Tilton said their bearing should work as long as it will fit in the center of the weights. The OD of the bearing portion of the hydraulic assembly is the same as the throwout bearing I have been using so it should be good, and so far it seems to be, as I have about 200 miles on it with no issues.
The master cylinder is a kit, with two reservoirs and the option of remote mounting the reservoir so it pretty well covers all bases.
The bolt pattern of the master cylinder is vertical, rather than horizontal, like stock. The positioning and height of the reservoir require that the cylinder be spaced out about 2 5/8" from the firewall. So I got to work on an adapter to accomplish both.
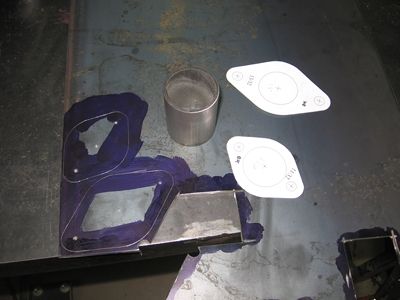
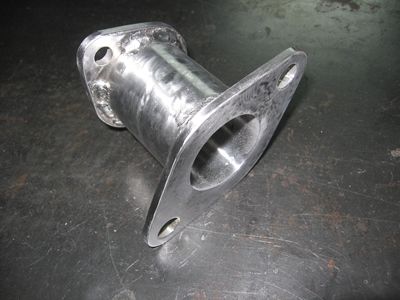
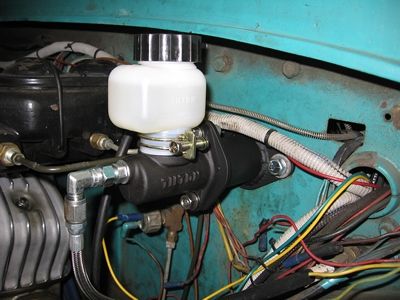
I forgot to get a picture of the bearing with it on the input bearing retainer and before mounting the transmission to the engine but this one shows most of what you need to see. The kit comes with a bolt to replace one of the bearing retainer bolts. That bolt is threaded for a smaller diameter shoulder bolt that locates the assembly to keep it from rotating. The bearing can be installed with the hydraulic lines going to the driver's side or passenger's side, whatever you need for your application. Whichever line is at the top is used for bleeding.
In this picture you can also see the counterweights I mentioned earlier, the rectangular things positioned around the bearing.
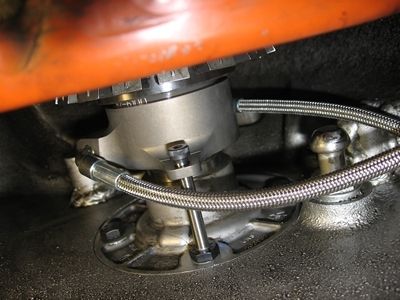
Now to plumbing. I was able to use the same hose that I was using and only needed a couple fittings to join everything. The master cylinder has a 3AN female outlet. The Bearing has 4AN female on each hose. The hose I have been using is 4AN, female on both ends. So I needed a 3AN to 4AN fitting for the master cylinder, a 4AN right angle fitting from there to the hose and to join the hose, to the bearing, I used a 45 degree 4AN bulkhead fitting, which allows me to mount the line to the bell housing, in the place of the slave cylinder, via a bracket. This time I made the brackets out of Aluminum instead of steel.
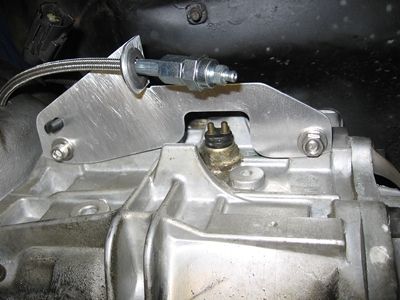
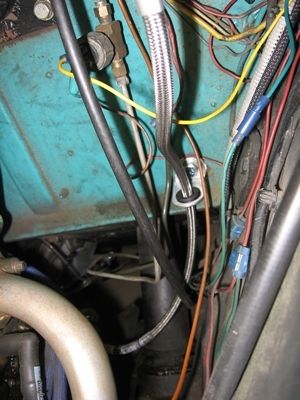
The master cylinder comes with a 5/16-24 threaded pushrod. To connect that to the pedal, I used a rod end, a coupling nut, and some jam nuts. The rod end comes with a 5/16" bore. The stock bolt is 3/8" so there is a 1/16" difference to handle. For that, I cut a spacer out of some 3/8" .028 wall DOM tubing. DOM tubing has no weld seams and is useful for making spacers such as this one. The spacer is as thick as the pedal, 5/16".
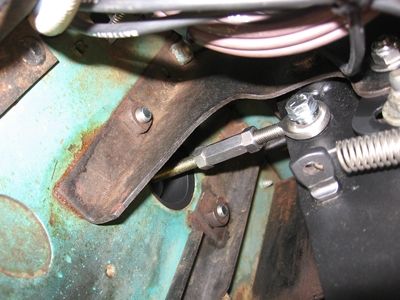
The way I adjusted the pedal resulted in it being quite a bit lower than before. Tilton say that a return spring is not necessary unless there is too much friction in the pedal linkage to allow the pedal to return, but I think it is a good idea to incorporate that if you can. The lower pedal height requires that the bumper be re-positioned. So I mad a bracket that mounts in the stock slot and allows for the additional adjustment needed.
An alternative way is to make a stop for the pedal at the bottom of it's travel. Then you can adjust it for the same height you had and the stock bumper will work fine.
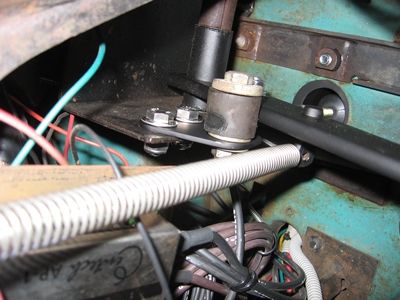
Currently on the drawing board is a grommet to fit the clutch fork hole, to keep the lines from contacting the bell housing.
When compared to the oem setup:
Pros
-More easily found replacement parts
-Very light pedal, and extremely smooth
-Slightly more room for exhaust, turbos, whatever non stock things you may want to fit under the hood.
Cons
-More expensive
-Custom parts required for proper installation
Key Parts list:
From Summit
TIL-75-875U Master Cylinder
TIL-60-6104 Hydraulic Bearing for T5
EAR-64191922ERL 4AN Hose
AER-FBM2749 3AN to 4 AN adapter
EAR-966304ERL 4AN 90° swivel fitting
FRA-583704 4AN 45° bulkhead fitting
FRA-592404 4AN bulkhead nut
QA1-GMR5T Rod End
Possibly:
AAF-ALL50855 Bleeder caps
From BMW:
34 32 1 233 159 Hose Grommets
What was happening is that the clutch fork wears into the throwout bearing collar. The clutch I'm using is about 1/2" thinner than stock and I think that may be causing geometry issues and causing the wear. I think the fix for this is to have a longer or adjustable fork pivot stud made. Since the truck Y-Blocks use a 9/16 thread for the pivot stud, there is nothing from any other engine that I'm aware of that can work to do that. This means that stud would have to be custom, and therefore expensive. By itself, that is probably the way to go. However, because I had other issues, doing that to stick with the stock stuff wouldn't be very cost effective.
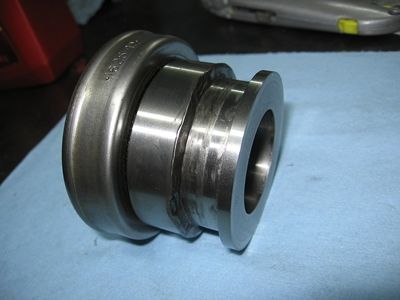
I got a master cylinder kit and hydraulic bearing from Tilton Engineering. There are others but for some reason, a lot of these bearings are indicated to not work with counterweight assisted pressure plates. Since that is what I have, Centerforce Dual Friction, it must work with that and Tilton said their bearing should work as long as it will fit in the center of the weights. The OD of the bearing portion of the hydraulic assembly is the same as the throwout bearing I have been using so it should be good, and so far it seems to be, as I have about 200 miles on it with no issues.
The master cylinder is a kit, with two reservoirs and the option of remote mounting the reservoir so it pretty well covers all bases.
The bolt pattern of the master cylinder is vertical, rather than horizontal, like stock. The positioning and height of the reservoir require that the cylinder be spaced out about 2 5/8" from the firewall. So I got to work on an adapter to accomplish both.
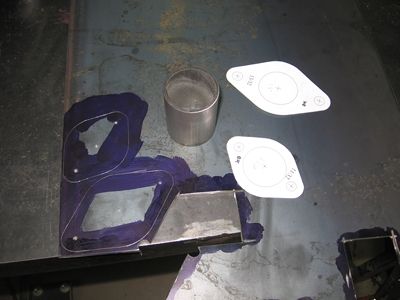
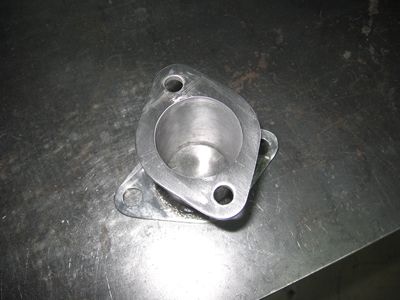
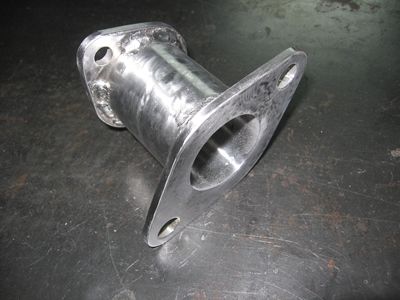
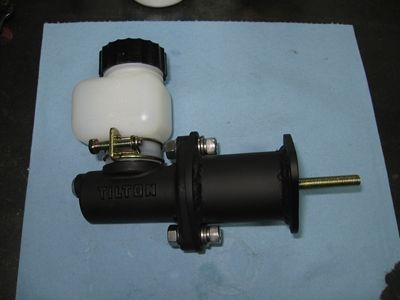
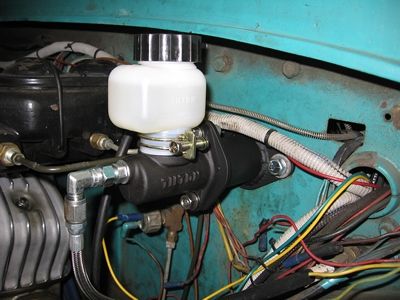
I forgot to get a picture of the bearing with it on the input bearing retainer and before mounting the transmission to the engine but this one shows most of what you need to see. The kit comes with a bolt to replace one of the bearing retainer bolts. That bolt is threaded for a smaller diameter shoulder bolt that locates the assembly to keep it from rotating. The bearing can be installed with the hydraulic lines going to the driver's side or passenger's side, whatever you need for your application. Whichever line is at the top is used for bleeding.
In this picture you can also see the counterweights I mentioned earlier, the rectangular things positioned around the bearing.
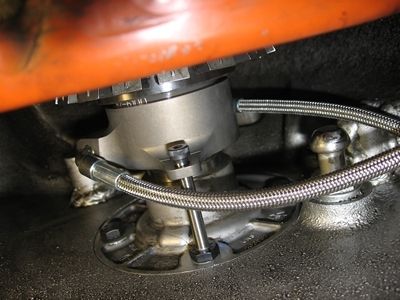
Now to plumbing. I was able to use the same hose that I was using and only needed a couple fittings to join everything. The master cylinder has a 3AN female outlet. The Bearing has 4AN female on each hose. The hose I have been using is 4AN, female on both ends. So I needed a 3AN to 4AN fitting for the master cylinder, a 4AN right angle fitting from there to the hose and to join the hose, to the bearing, I used a 45 degree 4AN bulkhead fitting, which allows me to mount the line to the bell housing, in the place of the slave cylinder, via a bracket. This time I made the brackets out of Aluminum instead of steel.
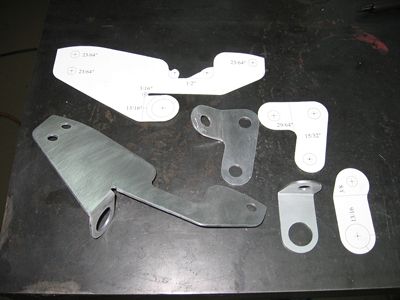
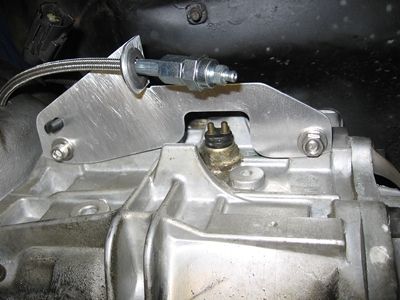
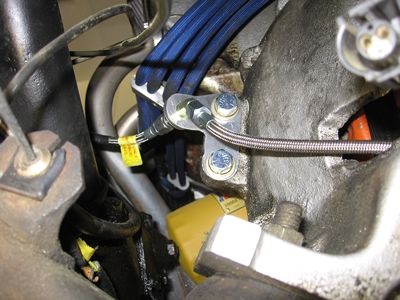
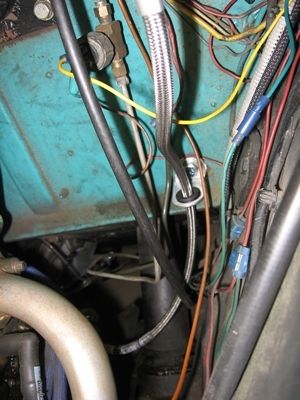
The master cylinder comes with a 5/16-24 threaded pushrod. To connect that to the pedal, I used a rod end, a coupling nut, and some jam nuts. The rod end comes with a 5/16" bore. The stock bolt is 3/8" so there is a 1/16" difference to handle. For that, I cut a spacer out of some 3/8" .028 wall DOM tubing. DOM tubing has no weld seams and is useful for making spacers such as this one. The spacer is as thick as the pedal, 5/16".
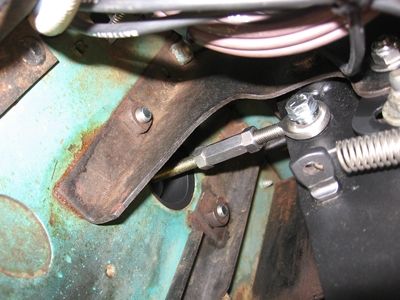
The way I adjusted the pedal resulted in it being quite a bit lower than before. Tilton say that a return spring is not necessary unless there is too much friction in the pedal linkage to allow the pedal to return, but I think it is a good idea to incorporate that if you can. The lower pedal height requires that the bumper be re-positioned. So I mad a bracket that mounts in the stock slot and allows for the additional adjustment needed.
An alternative way is to make a stop for the pedal at the bottom of it's travel. Then you can adjust it for the same height you had and the stock bumper will work fine.
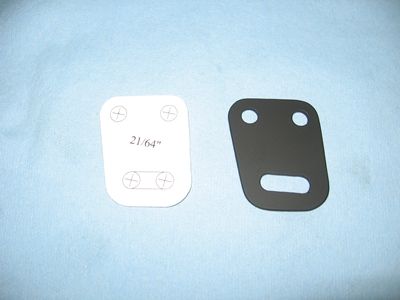
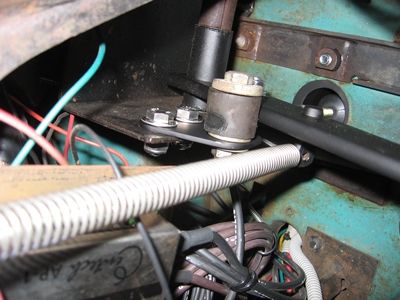
Currently on the drawing board is a grommet to fit the clutch fork hole, to keep the lines from contacting the bell housing.
When compared to the oem setup:
Pros
-More easily found replacement parts
-Very light pedal, and extremely smooth
-Slightly more room for exhaust, turbos, whatever non stock things you may want to fit under the hood.
Cons
-More expensive
-Custom parts required for proper installation
Key Parts list:
From Summit
TIL-75-875U Master Cylinder
TIL-60-6104 Hydraulic Bearing for T5
EAR-64191922ERL 4AN Hose
AER-FBM2749 3AN to 4 AN adapter
EAR-966304ERL 4AN 90° swivel fitting
FRA-583704 4AN 45° bulkhead fitting
FRA-592404 4AN bulkhead nut
QA1-GMR5T Rod End
Possibly:
AAF-ALL50855 Bleeder caps
From BMW:
34 32 1 233 159 Hose Grommets
Lawrenceville, Ga
1961 F100 Unibody
318 Y-block (292 +.070 bore, +.170 stroke), FMS T5-Z w/Mustang 10.5" diaphragm clutch.
1961 F100 Unibody
318 Y-block (292 +.070 bore, +.170 stroke), FMS T5-Z w/Mustang 10.5" diaphragm clutch.
- charliemccraney
- Posts: 1743
- Joined: July 9, 2008, 10:02 pm
- Location: Lawrenceville, GA
Re: Hydraulic Clutch
There's not much more to post about it. It's done and works.
Since the clutch springs also have an effect on the holding capacity of the clutch, they (or it in the case of a diaphragm clutch) cannot really be changed.
A lighter pedal also was not the goal, though it is nice that it turned out lighter as well.
Since the clutch springs also have an effect on the holding capacity of the clutch, they (or it in the case of a diaphragm clutch) cannot really be changed.
A lighter pedal also was not the goal, though it is nice that it turned out lighter as well.
Lawrenceville, Ga
1961 F100 Unibody
318 Y-block (292 +.070 bore, +.170 stroke), FMS T5-Z w/Mustang 10.5" diaphragm clutch.
1961 F100 Unibody
318 Y-block (292 +.070 bore, +.170 stroke), FMS T5-Z w/Mustang 10.5" diaphragm clutch.